A Complete CNC Milling Guide
When you develop a part of a whole assembly, your primary goal is to see it travel from your screen or a sheet of paper to reality. The design should be aimed at manufacturing intent. Otherwise, it would be science fiction like “The Time Machine” by H.G. Wells. To avoid your design becoming fictional, it is important to know what kind of manufacturing processes are out there. To help you with that, here is a CNC Milling service Guide.
What CNC Milling Is About Generally
There are lots of different manufacturing techniques out there that cast, bend, evaporate, heat, and do other things to achieve the desired form of material. CNC machining is a cutting technique. There is a revolving cutting tool present. It revolves and travels over a static clamped part ( in some variations, the table with the part lets the tool travel over the part). The part must be clamped tight or it will be removed by the cutting forces. The tool contains multiple cutting edges that remove chips from the material. As the tool completes its path along with the blank, you achieve the desired shape. That is the most basic description, but there are tons of nuances. That’s why machinists study the craft all their lives.
CNC Milling Process
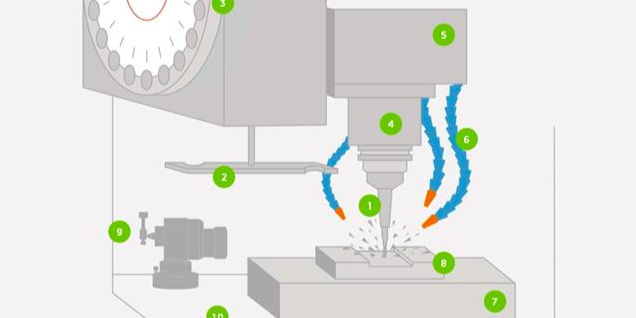
- Installing the tools into the tool holder. The machinist looks at the NC program and loads all the required tools into the tool holder so that their change can commence automatically during the cutting process. The machinist must determine tool offset (where tools end in the coordinate system of the machine tool) and enter them into the system.
- The machinist must set up the jigs and fixtures for the CNC machined parts. If the tooling is large, the machinist must enter its coordinates into the system to prevent collision with the tool.
- The machinist matches the zero point of the current CNC program with the zero of the machine tool. That is done to tell the milling machine where the blank is and where the cutting should take place.After that, the machinist clamps the blank. In some cases, step 3 comes after clamping. And then the CNC milling process occurs. There may be some additional steps with more complex parts or when batch machining is required but the general sequence is as described.
Types of CNC Milling Operations

There are multiple types of milling operations.
- Face milling. Face milling is a basic milling operation where the main cutting is done by the end of the mill. During face milling, the axis of the cutter is normal to the surface of the CNC milled part. Face mills usually have a large diameter to cover the most area. Or a ball nose end for complex surfaces.
- Plain milling opposite to the face milling happens when the side of the mill cuts the surface of the part. With longer mills, longer sides can be milled and with larger mills, more areas can be covered.
- Angular milling. Angular milling is convenient for deep pockets and concave surfaces. The mill axis is at a constant angle to the machined surface. That gives the advantage to reach deep areas with a shorter tool.
- Form milling. Form milling is the rarest compared to other methods. It requires a special tool. Usually, form milling is used to make gears, or to make convex and concave grooves, fillets, chamfers, and so on. CNC milling for prototyping rarely uses this technique, as it is expensive and is not very efficient.
CNC Milling Equipment
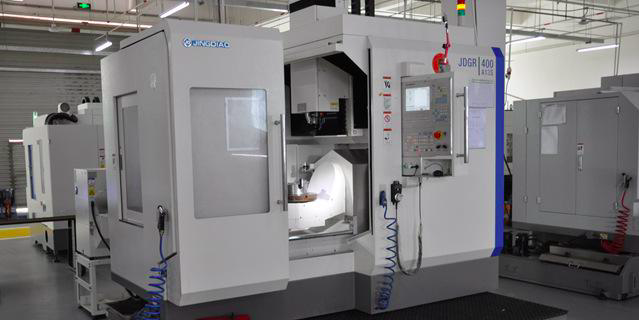
The main equipment for CNC milling is the CNC milling center. The main parameter that determines the capabilities of a milling tool is the number of axes. A basic CNC milling tool has 3 movement axes: XYZ. A 4-axis machine tool can turn around one of the axes to achieve a better orientation of the tool. a 5-axis machine tool can swivel around 2 axes and can manufacture virtually any surface with a very tight tolerance and surface finish.
The majority of machining centers have the same basic components: an interface, a column, a knee, a saddle, a worktable, a spindle, an arbor, a ram, a machine tool. However, depending on the configuration of the components, the CNC may differ in type.
Types of CNC Milling Machines
- Knee-type. These machines were the first milling machines designed. The spindle of the tool is fixed and the worktable moves horizontally in the saddle and vertically with the knee. Such machine tools offer good rigidity and precision.
- Ram-type. With ram-type CNC milling tools, the worktable only moves up and down but the spindle is fixed on a moving block- the ram. It moves along the horizontal axes and ensures that the tool reaches where it must.
- Bed-type. Here, the worktable is fixed and all the movements are made by the spindle connected to a coordinate device. If you add two swivel motions- one to the worktable, the other to the spindle, you can easily get a 5-axis CNC machine.
- Planer-type
CNC Milling Tools
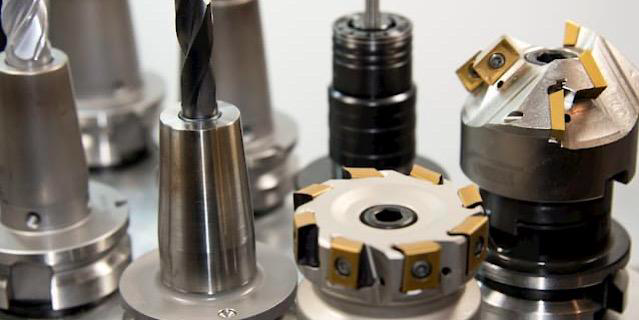
CNC cutters are called mills and there is a large variety you can use depending on the material and the precision. The basic option is the end mill. It can manufacture the majority of simple surfaces in milling. If you need complex surfaces, you can use the ball nose mill. In both cases, the end of the mill plays the main role in the cutting process. It is flat for the end mill and spherical for the ball nose mill. CNC machining of prototype parts is mostly done by those two. However, for batch machining, you can use a face mill and a cylinder mill. Both of them produce flat surfaces with increased efficiency compared to the end mill. They simply have a larger surface area. In some specific cases, special tools such as thread mills, chamfer mills, and modular mills are used.
Depending on the mill geometry, you can efficiently machine different materials. For instance, a two-flute mill is great for machining aluminum but titanium parts require a lot of flutes. Some materials stick to the tool and need chip breakers along with the flute.
CNC Milling Material Considerations

One of the advantages of CNC milling is the capability to process almost any kind of material. CNC milling can process all kinds of steel, titanium alloys, aluminum alloys, tungsten, copper, bronze, iron, all kinds of wood, different glass types. The majority of plastics can be milled as well. You should look out for flexible types though. You may have to freeze them or they will bend away from the machine tool. Depending on the part material, you should carefully choose the milling cutter and the cutting parameters.
Milling vs. Alternative Processes
CNC milling is evidently not the only way to process materials. Other similar methods involve turning, grinding, and EDM machining. So, when should you choose milling, and when – look elsewhere? CNC milling is perfect for its flexibility in part manufacturing. When turning is more useful for revolution parts, milling is great at making all kinds of elements. Milling is great when you need to chip off a lot of material, whereas grinding and EDM machining cannot cope with a lot of material to process. However, milling has its limitations, you can’t achieve a tolerance closer than IT6.
Summary
This was the CNC milling guide. We hope it will be useful to all the designers who are making things for manufacturing and haven’t been too clear on the process to choose from. If you have a CNC milling project, please don't be hesitate to contact us info@waykenrm.com
To find more information on our latest blogs related to CNC milling topics, you may don't miss as bellows:
- CNC Milling Services: What Do You Pay For?
- 4 Common Workpiece Defects and Their Causes in CNC Milling
- Machining Projects by CNC Milling
- CNC Milling in the Production of Automotive Parts