How Accurate Are 3D Printers? Exploring the Benefits and Limitations
What is 3D Printing?
In the age of advanced technology, 3D printing is considered one of its most crucial and revolutionary advancement. 3D printers make it possible to print three dimensional objects with great precision and accuracy. Despite this, there are always questions about how accurate these 3D printers can be. How close will these prints come to the real object? In this blog post, we'll explore the accuracy levels of 3D printers as well as some of the benefits and limitations they have. By looking at the accuracy of 3D printers, we can get an even better understanding of the engineering and technology behind them. Buckle up and get ready - let's dive into it!
3D printing is a process of making three dimensional solid objects from a digital file. It can be compared to more traditional forms of manufacturing, such as subtractive manufacturing techniques like milling and drilling, which involve precision cutting or drilling material away from a blank piece of metal or plastic until the desired object is formed. In contrast to these traditional techniques, 3D printing adds layers of material together in one continuous loop to create an object. In this way, using only a minimal amount of resources such as raw materials and energy, 3D printing can rapidly produce components with complex geometries without any tooling necessary.
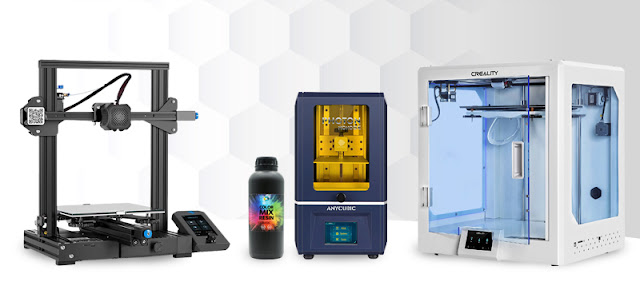
At the same time, 3D printing also has its limitations when it comes to accuracy. Depending on the type of technology being used as well as the nature of the part being produced, 3D printed parts may have defects or inaccuracies which would be unacceptable in other manufacturing processes. In addition, while some technologies allow for production speeds that are competitive with more traditional methods, others take substantially longer, meaning that certain parts may require additional post-processing steps before they can be considered production-ready.
For these reasons, 3D printing has become an increasingly popular option for prototyping and short-run production jobs. As research and development in this field continues to expand, however, we could start to see wider acceptance of 3D printing for larger and more accurate production needs in not just prototyping but mass production scenarios as well.
As complex and varied as the world of 3D printing is though, understanding how it works is crucial to being able to reap the full benefits of its technology. And so with that in mind, let's take a look at exactly how 3D printers make those objects we use every day.
How Does 3D Printing Work?
3D printing is a process which involves the use of digital files, computer-controlled machinery, and additive manufacturing techniques to create three-dimensional objects from plastic, metal, or other materials. It is an increasingly popular way to quickly create accurate prototypes and even fully functional products, without requiring the myriad tools and molds associated with traditional methods of fabrication.
At its core, 3D printing works by layering thin layers of material one on top of the other until the desired object is formed. The process is initiated by first creating a design in 3D modeling software or through scanning physical protypes with a 3D scanner. This raw data can then be manipulated into a 3D design file format and sent to the printer where it will be processed. The most common type of 3D printer uses a plastic extrusion method where molten plastic filament is fed into the printer nozzle and laid down onto the build platform and a laser beam solidifies it into shape according to the instructions set forth in the design file. For more intricate objects, multiple layers of PLA or ABS plastic are fused together through a heating process.
Read more about best printer for small businesses.
Though 3D printing offers many advantages such as faster turnaround times, improved accuracy, and lower costs compared to traditional methods of fabrication, there are also some limitations users should be aware of when using this technology. Undeniably, the most significant limitation faced by consumers and businesses alike is the material composition used in 3D printing processes, as certain types may be better suited for specific applications than others. As such, careful consideration must always be taken when choosing which materials should be used for any given project.
But despite these drawbacks, 3D printing remains an incredibly powerful tool for bringing ideas off paper and into reality with unprecedented accuracy. Its continued development over recent years has enabled people from all backgrounds to enjoy greater access to high-quality prototyping services than ever before—a trend that looks set to continue as new technologies such as stereolithography enter the market. As we prepare for an evermore digitized world, it's no wonder that 3D printing will be playing an ever larger role in bridging our visions with reality. To explore how this exciting technology actually accomplishes this task on a deeper level, we now turn our attention towards its layer-by-layer fabrication process.
Layer-By-Layer Process
The process of 3D printing is often described as layer-by-layer manufacturing in order to give people a better sense of how the technology works. This method of manufacturing is highly refined and quite different from traditional methods. With 3D printing, the object being printed is built up layer-by-layer on top of the existing model. This is done by depositing successive layers of material, such as plastic filament or metal powder, that are fused together using heat or chemicals to form the desired object.
Advocates of 3D printing argue that this method has numerous advantages over traditional machining techniques like milling and drilling. For one, layer-by-layer printing eliminates restrictions associated with CAD designs, allowing for more intricate shapes and details than ever before. Furthermore, because parts are being built up material can be placed exactly where it is needed, reducing overall material waste and cost. The process also eliminates the need to use cutting tools which usually cause a lot of vibrations, therefore resulting in higher accuracy.
On the other hand, some industry professionals are skeptical about layer-by-layer construction when it comes to precision parts due to the fact that each layer may suffer from minor errors which accumulate over time resulting in dimensional inaccuracy at the finished product. Regardless, numerous industries ranging from medical to aerospace have been able to maximize their operations with this game-changing technology by incorporating it into their own production lines.
Ultimately, due to its ability to produce complex objects quickly and accurately with minimal waste and material usage, layer-by-layer printing has become an essential tool in both prototyping and mass production processes; however, nothing is perfect and there will always be room for improvement when it comes to accuracy. With that said, let's now turn our attention towards another potential problem associated with 3D printing: measurement accuracy.
- Most consumer-grade 3D printers have an accuracy of around 0.1 mm or less for the X, Y and Z axes.
- The accuracy of a layer in a 3D printed part can depend on many factors, such as direction, temperature and speed.
- According to a study, the average layer by layer printing resolution of all available Fused Deposition Modeling (FDM) 3D printers is 0.13 mm in all directions.
The Measurement Accuracy of 3D Printers
The measurement accuracy of 3D printers is one of the most important considerations when selecting a 3D printer. Because 3D printing works by adding layer-upon-layer together, millimeter level accuracy must be achieved to maintain a correctly proportioned object. Even small deviations in the layers can lead to dimension inaccuracies, which could negatively impact the usability and aesthetic appeal of the final product.
Generally speaking, the measurement accuracy of 3D printers tends to depend largely on their build size and the quality of the components used. On average, FFF/FDM 3D printers tend to have an accuracy deviation of between 0.2 mm and 0.3 mm per 100 mm, SLA/DLP Printers tend to range from 0.05 mm - 0.15 mm per 100 mm; and SLS 3D printers typically print with a variation of around 0.1 mm - 0.3 mm per 100mm. However, variations within these ranges are quite common depending on various factors such as calibration accuracy, nozzle size, material used etc.
In addition, there are other considerations when it comes to measuring and recording dimensions accurately with a 3D printer. For instance some engineers will use G code to precisely control geometric properties such as bridging (flow rate), overhang angle and wall thickness; while also taking into account temperatures and time related measurements (i.e., time taken for each layer to cool down). By doing this they can create objects that very closely resemble their CAD designs but more importantly - are held together securely in the correct form factor when finished.
This has been a brief exploration into the measurement accuracy of 3D printers and how it might influence the success or failure of creating a functional object from your design file. As with any technology or manufacturing process there are always certain elements that must be taken into consideration in order to ensure produced parts meet customer requirements and quality standards. With this understanding we move onto considering how 3D printers can be used to measure and record dimensions accurately, as well as what other features need to be taken into account in order for consistent part performance during production runs today - some amazing examples of which we'll discuss next..
Measuring and Recording Dimensions
When it comes to measuring and recording dimensions, 3D printing is an invaluable tool. Not only does it make it easier to find the exact measurements a designer or engineer needs, but they can also be accurately recorded and repeated multiple times, making it perfect for prototyping and product development.
When seeking accuracy in measurements, there are several factors to consider when using 3D printers. First, most 3D printers have a pre-set layer resolution that affects the surface finish of your final product. The higher the layer resolution—or number of layers per given unit of distance—the more accurate the data that’s recorded by the printer. In addition, the printer must maintain a consistent temperature throughout the printing process which must be controlled through the use of cooling fans or blowers.
Then there are other variables at play that could affect measurements including nozzle size, print speed and material type. Since these variables may differ from machine to machine and project to project, it is essential for makers to always test and calibrate their machines to ensure accuracy with each new project.
Ultimately, 3D printing offers a unique opportunity for makers to measure and record accurate parts with relative ease. It’s also important to remember that no level of preparation can guarantee 100% accuracy as operating conditions might change during or between jobs. As such, it is essential to remain vigilant when measuring and recording parts close tolerance applications on any 3D printer. With this in mind, let's explore the different types of materials used in 3D printers and how they each impact the final results.
Comparing Different 3D Printing Technologies
When exploring the accuracy of 3D printing, it is important to consider the different technologies available and how they affect the quality and accuracy of the product. The major 3D printing technologies are direct metal laser sintering (DMLS), fused deposition modeling (FDM), three-dimensional printing (3DP), selective laser melting (SLM), and stereolithography (SLA). Each of these processes has advantages and disadvantages as well as different levels of accuracy.
Direct metal laser sintering is a highly accurate method that uses lasers to heat metal particles in order to create finished products. It is precise because it relies on exact measurements that have been measured and calculated beforehand. On the other hand, its primary disadvantage is that product alterations or improvements are not possible once the process has begun.
In contrast, fused deposition modeling or FDM is much less accurate than DMLS but can be used for a wider range of applications due to its lower cost and improved flexibility. Additionally, FDM allows for easy post-processing of 3D parts via sanding, polishing, and dyeing. However, this technique produces a lower surface finish than many other printers, which can impact overall precision in some scenarios. Due to this limitation, FDM should generally be used with more basic parts that do not require very high accuracy levels.
Three-dimensional printing or 3DP is also relatively inexpensive compared to other methods, although it is still associated with trade-offs in terms of accuracy. This process involves layers being deposited on top of each other until the desired object shape is achieved; however, small imperfections can appear in both single layers and at joints between multiple layers. On the other hand, this process can provide unique opportunities for one-off custom products or batch production by manufacturing many copies of complex designs rapidly.
Selective laser melting and stereolithography are two other commonly used technologies for fabricating 3D prints with higher accuracies at greater costs. SLM works by precisely melted materials such as metals into molds; whereas, SLA utilizes lasers to harden liquid plastics into objects with great precision. Unlike FDM however, these processes produce almost zero waste material which results in quicker completion times as well as cost savings due to the reduction in additional resins required during fabrication.
Overall, depending on specific needs, there are a number of viable options when considering different 3D printing technologies for improved accuracy and efficiency - ranging from lower cost methods such as FDM to higher end implementations like SLM and SLA. By understanding which techniques work best for certain applications, manufacturers have an easier time achieving their desired outcomes while also maintaining budget constraints when producing quality products in a timely fashion. With this knowledge in hand we'll now turn our attention to explore how digital fabrication machines compare against more traditional methods of creating physical objects.
Digital Fabrication Machines Compared
In the previous section, we looked at the different 3D Printing technologies available and explored their capabilities. However, there is much more to digital fabrication machines than just 3D printers. When comparing digital fabrication machines, it’s important to also consider CNC milling machines, laser cutters and engravers.
CNC milling machines are great for cutting complicated shapes from hard materials such as aluminum or steel. Unlike 3D printers which use plastic filaments, CNC milling machines can achieve tighter tolerances and smooth finishes with metals. Laser cutters create very precise designs by burning away material with a focused laser beam. The parts created with a laser cutter may not have smooth edges, but they are able to make intricate shapes with a precision that is not easily matched by other tools such as saws and routers. Laser engravers create designs on surfaces by utilizing the same technology as a laser cutter in a different way. Engravers can be used for branding and labeling products, creating patterns on wooden surfaces, and making signs for businesses.
Each of these digital fabrication technologies offers its own advantages over traditional tools and methods of fabricating parts. For example, 3D printing has the potential to reduce production costs as well as lead time--which make it an attractive option for smaller scale prototyping or producing custom parts in low quantity orders. On the other hand, CNC milling machines are better suited for high volume orders due to the greater accuracy and precision of cuts despite being limited to cutting metal materials instead of plastic or resin like some 3D printers are capable of doing. Ultimately, it's important to determine your budget and needs when considering any type of digital fabrication machine—as each technology carries its own set of benefits and limitations that could be beneficial depending on the project at hand.
No matter which fabrication technology you choose--ultimately, it all comes down to finding a balance between cost and quality without sacrificing either one too far. As we transition into exploring the benefits and uses offered by 3D printers specifically--let’s take what was learned in this section about digital fabrication machines in general into account when moving forward.
Benefits and Uses of 3D Printers
The benefits and uses of 3D printers are abundant. Being able to rapidly produce physical objects that perfectly integrate the design intent enables efficient exploration of product ideas and creations. These capabilities have opened a whole new world for the advancement of technology, with many industries finding uses for 3D printing in areas such as rapid prototyping, architecture, medicine, education, engineering, manufacturing, aeronautics, automotive, aircraft parts, and even food production.
Rapid prototyping with 3D printers is an especially useful benefit that has been embraced in several industries. It allows designers to quickly create highly-accurate physical objects to be tested by engineers. Applying this practice shortens the development process significantly. Since 3D printers can easily produce relatively complex geometries and details—unlike traditional fabrication methods—this increases the precision and quality of prototypes produced. Additionally, using 3D printers ensures consistency across multiple versions due to their accuracy and repeatability while also reducing costs associated with materials since only what is necessary is used to build the object.
Medical industries have benefited from the usage of 3D printing in several ways. Simulations of patient anatomy created through CT scans or MRI data have enabled medical professionals to accurately measure potential treatments or surgical plans with greater precision than ever before. Additionally, 3D printing has revolutionized the prosthesis industry by allowing for custom-fitted pieces that not only look better but also feel more comfortable for users compared to traditionally manufactured equivalents. Finally, life-saving applications of 3D printing such as artificial organs are constantly being researched and improved upon while also showing great promise in becoming viable treatments in the near future.
To sum up, 3D printing is widely enjoyed in many industries due to its ability to quickly bring designs into physical reality without sacrificing accuracy or quality when done correctly. Industries such as rapid prototyping and medicine have found great success in utilizing this technology which can be expected to expand further as more applications are discovered and cost becomes less of a barrier for widespread adoption in other sectors as well.
Frequently Asked Questions Answered
What is the most accurate 3D printer currently on the market?
The most accurate 3D printer currently on the market is the Prusa i3 MK3S. It has a layer resolution of 0.04mm and a print accuracy of 0.2mm for producing highly detailed parts with incredible accuracy. This level of precision is achieved through its finely tuned extrusion system, advanced linear motion system, sensor feedback supporting auto bed leveling, and the implementation of a heated bed that aids with adhesion during the printing process. By utilizing components designed specifically for 3D printing, it is able to create prints which exhibit an improved surface quality, superior detail, and produces less warping than competing models on the market today.
What is the standard measure of accuracy for 3D printers?
The standard measure of accuracy for 3D printers is typically given in terms of the resolution and tolerance of the printer. Resolution refers to the minimum layer height achievable by the 3D printer and is measured in microns. Tolerance, on the other hand, indicates how closely an object can be replicated from a digital file or model. This is usually measured as an average deviation from the intended shape, size or design of a 3D printed object in either millimeters or microns. A high-resolution and precise tolerance are important factors when measuring the accuracy of a 3D printer.
What factors affect the accuracy of 3D printer output?
There are several factors which affect the accuracy of 3D printer output. Firstly, the accuracy level within the 3D modelling software. If the software was created without a high enough level of accuracy then this can result in errors when transforming 2D pictures into 3D models. Secondly, accuracy is affected by the type of filament being used and its extrusion temperature. Low-grade filaments can produce lower quality prints, as well as incorrect measurements if not heated to the correct temperatures. Thirdly, issues with how the printer is set up can also affect accuracy - things like bed levelling and calibration, as well as nozzle height and calibration. Finally, environmental factors such as air humidity and airflow around the printer can also affect accuracy significantly.
How do different 3D printing materials affect accuracy?
3D printing materials can have a major impact on the accuracy of a 3D print. Different 3D printing materials such as PLA, nylon, and ABS will all result in different levels of accuracy. Generally, higher-temperature warping materials such as nylon and ABS are less accurate than lower-temperature non-warping materials such as PLA. This is because the high temperatures involved when using these materials can cause warping or shrinkage, resulting in distorted prints. Additionally, softer filaments like flexible TPUs become increasingly difficult to work with as they require higher levels of precision in order to achieve a successful outcome.
In contrast, harder materials such as metals and ceramics require very precise and controlled temperatures that often prove challenging for many 3D printer users. These materials take longer to reach the ideal temperature and cool down, further decreasing their accuracy capabilities. Furthermore, since these materials are more brittle than traditional plastic filaments, they are also prone to cracking or breaking if printed at too high of a speed or temperature setting which affects the accuracy of the print.
Overall, different 3D printing materials have different effects on the accuracy of the end product. Soft materials may be easier to work with but more prone to errors, whilst harder materials can take longer to reach optimal temperatures and potentially break during printing. It is important when choosing a material for a 3D project to consider all these factors and how they will affect accuracy.
How can I improve the accuracy of my 3D printer?
Improving the accuracy of a 3D printer involves numerous steps. Firstly, you should check the calibration and setup of your 3D printer. Make sure that all components, such as the build plate, are level and that all tension settings are properly adjusted. Additionally, you should ensure that your filament has been stored correctly and is free from contaminants to ensure a consistent supply of material. Improper nozzle diameter can also affect print accuracy. If you have any doubt regarding the dimensions of your nozzle, it might be worth getting a more precise one.
You should also consider upgrading to a higher-resolution print bed to increase accuracy. Pay special attention to printer bed adhesion since a poor adhesive layer on the bed can cause warping or delamination of prints. Using various slicer settings can also make a big difference in improving the quality and accuracy of your prints.
Finally, proper post-processing techniques like sanding or chemical treatments can help you get even better results from your 3D prints.